

Glazed and Fired:
Celadon Ceramics from the UMAG Collection
窯火純青:
香港大學美術博物館藏青釉器
Curated by Dr Florian Knothe, Kenneth Shing-Kwan Chan
Edited by Christopher Mattison and Kuldip Kaur Singh
策展人:羅諾德博士,陳承焜
文字編輯:馬德松,星家恩

Introduction
Pre-dating the Neolithic period, ceramic wares are some of the earliest man-made objects to integrate science, technology and the arts. A close examination of ceramics can reveal the creative advances of individuals in various cultures and time periods, and reflect a society’s broader development and technical progress.
With a long history of innovation and craftsmanship, celadon wares have provided a crucial reference point for the study of ceramic production in China. The term ‘celadon’ historically refers to specific types of ceramics coated with a green-coloured glaze. Taking its name from a French literary character best known for his distinctive green attire, some scholars prefer to avoid this arbitrary Western construction and instead apply the term ‘greenware’.
Constant advances in raw material selection, firing techniques and the shaping of forms have enabled celadon ceramics to develop continuously over the past two millennia. The UMAG collection of celadon spans a period of more than fifteen hundred years of celadon’s history, from the early lead-glazed pottery of the Han (漢朝; 206 BCE–220 CE) to the stunning Guan wares of the Song dynasty (宋朝; 960–1279 CE), providing a rich overview of the traditions and transitions of these widely-coveted objects.
導言
陶瓷器物歷史悠久,在新石器時代前便已開始出現,可以說是最早融合科學、技術和藝術的人造物。對陶瓷的深入探究,不但可以揭示人類在各種文化和時代中展現的創作力量,更能反映出社會的整體發展和技術進步。
而在悠久的創新和工藝史中,青釉器(Celadon)為中國陶瓷生產的研究提供了重要的參考依據。青釉器泛指塗有青綠釉料的陶瓷器物,而「Celadon」一詞則由法國文學中,一位身穿獨特綠衣的角色的名字衍生而來。一些學者為避免「Celadon」當中隱含的西方建構,而改用「Greenware」一詞。
在原材料的選擇,燒製技術和塑形技巧等方面的不斷進步,使青釉器在過去兩千年中得到持續發展。香港大學美術博物館擁有橫跨超過一千五百年的中國青釉器藏品,從漢代(公元前206–公元220年)的早期綠釉器到宋代(公元960–1279 年)的瑰麗官窯器,讓觀眾得以概觀這些廣受青睞的青釉器物的傳統和演變。


I. Han-dynasty Green-glazed Ceramics
I. 漢代綠釉器
Vase, Eastern Han dynasty (25–220 CE), Earthenware with green glaze. HKU.C.1953.0069
瓶,東漢 (25–220 CE) ,綠釉陶器.HKU.C.1953.0069
3D Model of the Han-dynasty Vase (HKU.C.1953.0069)
Creator: Tullia Fraser
漢代鉛釉瓶(HKU.C.1953.0069)的三維模型
設計者:韋莉雅
Created in the Eastern Han dynasty (東漢; 25–220 CE), one of this small vase’s (HKU.C.1953.0069) most significant characteristics is its lead-based, dark olive-toned glaze. Originally developed to replicate the colour and texture of bronze, some of the earliest examples of lead-glazed pottery (鉛釉器) imitating bronze are known from the end of the Warring States period (戰國時代; 475–221 BCE). Occasionally found in Western Han (西漢; 206 BCE–9 CE) tombs, the technique became increasingly popular in the later Eastern Han period (Vainker, 1991). As lead is highly toxic, the majority of excavated lead-glazed wares were created as mingqi (明器 grave goods), rather than as objects for everyday use. Lead glazes were also used in the Roman Empire around this time, though it is unknown whether there is any connection between these two traditions.
Lead-green is a low-temperature glaze that uses lead as a fluxing agent. Due to variations in local raw materials and glaze recipes, low-temperature lead-glazed pottery was created primarily in the northern section of China during the Han dynasty, whereas potters in Southern China mainly produced high-temperature calcium-glazed pottery (Wang et al., 2019). Exemplified by the brownish mottling on the vase’s surface, tints and impurities often appear in lead glazes as a result of a number of uncontrollable factors. The vase’s interior and base are left unglazed, a characteristic shared by many Han-dynasty ceramic wares. According to Trubner and Falk (1961), the consistent distribution of glazes on Han dynasty vessels was the result of potters applying the glaze materials from above, which resulted in the coverage of only the upper side and rim with glaze.
這件小瓶(HKU.C.1953.0069)於東漢時期(公元25–220年)製成,其深橄欖色鉛釉為最顯著的特徵之一。鉛釉器的誕生最初是為了模仿青銅的顏色和質感,而最早的鉛釉器出產於戰國時代晚期(公元前475–221年)。西漢(公元前206–公元9年)的墓穴中偶爾會挖掘出鉛釉器,而鉛釉器物在東漢後期更變得越來越流行(Vainker,1991)。鉛具有劇毒,因此大多數出土的鉛釉器,都是作為明器(陪葬品)而製成,而非用作日常用品。在相若的時期,羅馬帝國亦有使用鉛釉料,儘管至今尚未清楚知道這兩種釉料傳統之間,是否存在任何關聯。
鉛綠釉是一種使用鉛作為助熔劑的低溫釉料。在漢代,各地原材料和釉料配方的差異,引致中國北部主要製作低溫鉛釉陶器,而南方地區則以生產高溫鈣釉陶器為主的情況(Wang et al.,2019)。由於各種不可控制的因素,漢代鉛釉經常出現色斑和雜質,就如這件小瓶釉料表面上的褐色斑點。此小瓶的內部和底部均未上釉,而這是許多漢代陶器的共有特徵。Trubner 和Falk(1961)指出,由於漢代陶工一般會從上方施以釉料,使釉料僅能覆蓋容器的上側和邊緣,令漢代陶器的釉料有著相若的分佈。
Model of Dog, Han dynasty (206 BCE –220 CE), Earthenware with green glaze. Gift of Songyin Ge Collection, HKU.C.2020.2475
綠釉瓷狗,漢 (206 BCE –220 CE) ,綠釉陶器.松隱閣惠贈,HKU.C.2020.2475
With its upward-facing head, floppy ears, unflinching gaze and mouth open mid-bark, this glazed pottery figure (HKU.C.2020.2475) depicts a rather solid and spirited looking canine. The ceramic dog is covered with a finely crackled green glaze, while the underside has been left unglazed, revealing its reddish-brown clay body. Likely a highly desirable item at the time, the studded, elaborately designed collar suggests the animal had an affluent owner. The majority of Han dynasty ceramic dogs unearthed at sites across China were made in a static pose, with a small number shown walking or barking. For a similar green-glazed dog dating to the Eastern Han, see R. Krahl, Chinese Ceramics from the Meiyintang Collection, 1994, vol. I, p. 75.
In the Han dynasty, dogs were popularly used for hunting and as guards, and ceramic dogs served as guardians in the afterlife (Rotondo-McCord, 2005). It was common to bury figures of dogs, as people believed they would accompany the deceased. Earlier in the Shang period, it had been common to bury dogs alive in tombs—a practice which continued until at least the Western Zhou (Mair, 1988). The remains of two hunting dogs were discovered in the late fourth-century tomb of the fifth ruler of the state of Zhongshan during the Warring States period. By the time of the Han dynasty, live dogs had been replaced by glazed ceramic models.
此釉器模型(HKU.C.2020.2475)有著向上的頭部,下垂的雙耳,堅定的目光和張開的嘴巴,刻劃出一隻意氣風發、炯炯有神的小狗。這件釉器被充滿細裂紋的綠釉覆蓋,其底部未有施上釉料,展露出其紅褐色的粘土土體。小狗的頸部配戴著飾有鉚釘,精心設計的頸圈。這種頸圈很有可能是當時受歡迎的飾品,亦顯示出小狗也許有著一位富裕的主人。中國各地出土的漢代陶狗模型多數有著靜態的表現,少數則呈現步行或吠叫的姿態。與這件釉器相類似的東漢陶狗,可見於康蕊君,《玫茵堂藏中國陶瓷》卷一,1994年,75頁。
在漢代,犬隻經常肩負起狩獵和守衛等工作,而陶狗模型則被認為是亡者在冥界的守護者(Rotondo-McCord,2005)。當時,人們相信犬隻會在死後世界陪伴亡者,所以時常將狗隻與死者一同安葬在墓穴之中。在商代早期,將活狗埋入陵墓的情況十分普遍,而這種習俗至少持續至西周時期(Mair,1988年)。在戰國時代,中山國第五任君主的王陵中,便發現了兩隻獵狗的遺骸。直至漢代,釉面陶狗模型才取代活狗作為陪葬物。
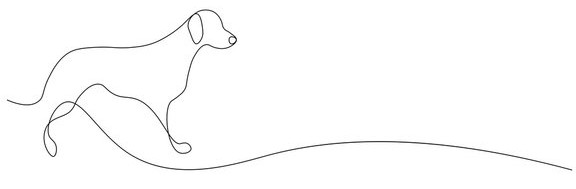
Watchtower, Han dynasty (206 BCE –220 CE), Earthenware with green glaze, Gift of Dr T. T. Tsui, Tsui Art Foundation Ltd. HKU.C.1996.1088.
瞭望台,漢 (206 BCE –220 CE) ,綠釉陶器.徐氏藝術基金公司徐展堂博士惠贈,HKU.C.1996.1088
Ceramic models of architectural structures were commonly included in Eastern Han tombs as a way to provide for the souls of the deceased. Green-glazed watchtowers (HKU.C.1996.1088) are among the largest ceramic objects to be excavated from Han dynasty tombs. Made of reddish-brown clay and covered with an uneven layer of lead-green glaze, this watchtower consists of four sections. Offering a rare glimpse into the building styles of the Han dynasty, the models include meticulous details, from the roof tile ends and corner ornaments to the miniature human figures standing at the windows.
東漢時期陵墓的明器之中,常常會包括建築物的陶器模型,予亡者之靈在冥界中使用。 這座綠釉瞭望台(HKU.C.1996.1088)是漢代墓穴出土的較大型陶製明器之一。這座瞭望台以紅棕色粘土坯體製成,被不均勻的綠釉層所覆蓋。整座綠釉瞭望台由四個部分組成,為中國漢代建築風格提供重要的參考依據。從屋頂設計與裝飾,到站在窗邊的微縮人物模型,整個建築物各部分的細節都塑造得非常仔細。
Well, Han dynasty (206 BCE –220 CE), Earthenware with green glaze, Gift of Ms Li Lai–wa, HKU.C.1997.1107
陶井,漢 (206 BCE –220 CE) ,綠釉陶器.李麗華女士惠贈 ,HKU.C.1997.1107
In addition to architectural structures, models of real-life objects, including pottery wells, mills, houses and pig sties were also regularly buried in tombs to provide for the deceased, who were believed to require provisions in the afterlife. Typically modelled with figurines of peasants and animals set within a granary, this well (HKU.C.1997.1107) and grain mill (HKU.C.2019.2490) models from the UMAG collection were likely produced as stand-alone grave goods. Ultimately, these burial objects worked in concert with other funerary goods to ensure the wellbeing of the dead in the afterlife. It is worth noting that the studded, circular ceramic disk of the grain mill model is unglazed, revealing the colour and texture of the clay body. It is unknown if the disk was never glazed, or if it delaminated over the centuries of burial.
漢代人們普遍相信冥界的生活與在世時相若。為了使亡者在冥界的生活能夠好一點,漢代的明器除了建築物陶器模型外,還包括陶井、石磨、居室和豬舍等模仿生前所用物品而製作的陶器模型。這些模仿日常用品的模型通常是居室明器的一部分,輔以民房、農民或動物型的微縮模型,以滿足亡者在冥界的起居生活。館藏的這件水井(HKU.C.1997.1107)和石磨(HKU.C.2019.2490)模型,很有可能作為獨立的明器而製作。這些種類繁多的明器互相補充,以確保死者在冥界可以過美滿的生活。這件石磨模型的突狀圓盤頂部沒有釉層,展現出粘土體的顏色和質感,其成因可能是陶工當時未有施釉,或是釉料在幾個世紀的埋葬過程中被剝離。
%20(1).jpg)
Grain Mill Model, Han dynasty (206 BCE –220 CE), Earthenware with green glaze. Gift of Claire and Francis Heritage Lane, HKU.C.2019.2490
石磨模型,漢 (206 BCE –220 CE) ,綠釉陶器.鴻踪里惠贈. HKU.C.2019.2490

II. Yue Celadons from the Han to Tang Dynasties
II. 漢代至唐代期間的越窯青釉器
Jar: bowstring pattern, Western Han dynasty (206 BCE – 9 CE), Earthenware with olive glaze, HKU.C.1964.0271
罐: 弦紋,西漢 (206 BCE – 9 CE) ,橄欖綠釉陶器.HKU.C.1964.0271
It is generally accepted that proto-celadon (原始青瓷) wares began to emerge in China in the Shang dynasty or earlier (Hao et al., 2013), gradually evolving into the Eastern Han’s so-called ‘true celadon’ (成熟青瓷). Most examples of proto-celadon vessels are relatively unrefined, with uneven thicknesses and glazes that include brownish spots and yellowish tints (Chen, 2004). Early true celadon wares exhibit some of the characteristics of porcelain, including a more refined slip and higher firing temperature, though they continue to display the basic patterns and shapes of proto-celadons. Scientific studies have shown that early true celadons were fired at a higher temperature and benefited from significant advances in kiln and firing technology, as well as from a profusion of refined decorative techniques such as impressing, moulding, carving and incising.
Produced in the Western Han dynasty, this large jar (HKU.C.1964.0271) epitomises an important milestone in the development of Chinese ceramics. Reminiscent of the forms of antique bronze vessels, the jar’s upper body is adorned with raised string patterns and a pair of handles in the shape of a wild beast’s head, which gives the jar its distinctive appearance. This particular olive-toned glaze is a type of high-fired glaze created in kilns in the Yuezhou (越州) area of northern Zhejiang province. Celadons produced in this region were later categorised as ‘Yue ware’ (越窯器), a name derived from the kiln’s location. A type of high-temperature glazed ceramic, Yue ware would lay the foundation for future celadons.
普遍認為,原始青瓷在商代或更早的時期開始出現(Hao et al.,2013),並逐漸演變成東漢時期所謂的成熟青瓷。原始青瓷的造工相對粗糙,厚度和釉料較不均勻,常帶有褐色斑點和淡黃色斑(Chen,2004)。儘管早期的成熟青瓷仍有著原始青瓷的基本圖案和形狀,它們亦具備一些與瓷器相同的特徵,包括更精緻的釉料和更高的燒成溫度。 根據科學研究所得,早期成熟青瓷在較高的溫度下燒製而成,其發展得益於窯爐和燒製技術的重大進步,以及壓印,模製,雕刻和切割等裝飾技術的廣泛開發。
這件大型陶罐(HKU.C.1964.0271)於西漢時期製成,印證著中國陶瓷發展的一個重要里程。 陶罐具有獨特的外型,其上腹部飾有凸起狀弦紋圖案,以及一對獸面形鋪首耳,外觀形態令人聯想到古代的青銅器皿。 陶器上覆蓋著一種特殊的橄欖色釉料,為浙江省北部越州窯區製作的一種高燒釉料。 這些於越州出產的青釉器被歸類為「越窯器」,其名稱取自窯爐的所在地。 越窯器是一種高溫釉面陶器,並為日後的青釉器發展奠定了不可或缺的基礎。

Vase , Eastern Jin dynasty (317–420 CE), Stoneware with celadon glaze, HKU.C.1964.0255
瓶,東晉 (317–420 CE),綠釉炻器.HKU.C.1964.0255
Yue ware objects produced in the Eastern Jin dynasty (東晉; 317–420 CE) (HKU.C.1964.0255) typically feature brownish-green or olive-coloured glazes, in stark contrast to the lead-green glazes from the Han dynasty. The Yue glaze was created with a mixture of clay, wood ash and sometimes a small amount of limestone (Wood, 1999). According to Phil Rogers (2003), it is possible that the introduction of siliceous rock into the glaze mixture contributed to this new and more refined finish. This vase is distinguished by its rounded neck and two small ring-shaped handles. The ceramic body is covered with a thin, somewhat lustrous, light olive-coloured glaze, with the glaze stopping just above the base. To achieve the colour, potters applied a mixture of clay and wood ash to the body and then fired the vase in a ‘dragon kiln’ (龍窯).
Arched and tunnel-shaped, the Yue dragon kilns were constructed from bricks placed along hillside slopes, which resembles the spine of a dragon. During the firing process, Yue potters placed the ceramics in the inclined firing chamber of the kiln, which connected the bottom firebox to the chimney situated at the top. The firing chamber served as a conduit for the fire’s heat and smoke and aided in the creation of a strong draft, thereby elevating the heat’s intensity to 1300°C—the temperature required to produce celadon glazes (Rotondo-McCord, 2001). While the area furthest from the firebox maintained a cooler temperature in early designs, stokeholes added to the sides of later kilns allowed fuel to be added during the firing, giving potters greater control over the temperature (Wood, 1999).
Yue potters also had to be aware of the levels of oxygen and other gases in the kiln. Within the dragon kiln, oxygen levels were monitored and controlled so that carbon monoxide and other gases could be channelled through the firing chamber to facilitate reduction firing, which is a precondition for achieving the Yue ware glaze (Rotondo-McCord, 2001). This reduction firing process added electrons to the metals contained in the glaze, primarily copper and iron, changing their colour and appearance and creating the range of shades referred to as celadon. This chemical reaction is crucial in the firing process, as the carbon monoxide and associated soot are primarily responsible for penetrating the glaze and creating the desired colours (Hamer, 2004).
東晉時代(公元317–420年)生產的越窯器(HKU.C.1964.0255)通常帶有棕綠色或橄欖色釉面,與漢代的鉛綠釉料有著鮮明對比。這種越釉由粘土、木灰和少量石灰石構成的混合物製成(Wood,1999)。 Phil Rogers(2003)的研究指出,釉料混合物還可能包含矽質岩石,而這種物質使釉面有著更細緻的外觀形態。此青釉瓶有著不同特點,包括渾圓的瓶體,一對環形小柄和淺橄欖色的釉面。 陶器的主體上覆蓋著一層薄薄的,略帶光澤的淺橄欖綠色釉面,釉料恰好停留在底部上方,青麗雅緻。 為了燒製這種特殊的釉色,越窯的陶匠將釉料混合物塗在瓶體上,然後在「龍窯」中燒製而成。
越州龍窯沿傾斜山坡,以磚砌築而成,窯體為呈拱形的長條形隧道,其外形似臥龍,故而得名「龍窯」(Roger,2003年)。 燒製的過程中,越窯工匠將陶器放入窯體中的傾斜燒製室。燒製室與底部的火爐和位於頂部的煙囪互相連接,不但為窯體輸送火源與煙灰,更能使窯內產生強烈氣流,有助將火的強度提升至生產青瓷釉所需的攝氏1,300度(Rotondo-McCord,2001年)。 在早期的龍窯設計中,距離火爐最遠的區域有著較低的溫度,而後期窯體側面添加了額外的爐膛口,使陶器工匠可以在燃燒過程中添加燃料,從而更好地控制窯內溫度(Wood,1999年)。
越窯工匠還必須時刻留意窯中氧氣和其他氣體的含量。 在龍窯內,氧氣含量受到監察和控制,使一氧化碳和其他氣體可以通往燒成室,以促成還原燒成的步驟。還原燒成這個過程是燒製越窯青釉的重要條件(Rotondo-McCord,2001),過程中會將電子(electrons)附加到釉中所含的銅及鐵等金屬中,從而改變它們的顏色和外觀,並形成被稱為青瓷的釉色色域。 這種化學反應在燒製過程中至關重要,因為一氧化碳和相關的煙灰主要負責滲透釉料,以產生所需的釉色色域(Hamer,2004年)。

Jar: lotus petals, Six Dynasties period (220–589 CE), Stoneware with celadon glaze, HKU.C.1969.0334
罐: 蓮瓣紋,六朝 (220–589 CE),綠釉炻器.HKU.C.1969.0334
The spread of Buddhism was one of the most significant socio-cultural changes to occur during the Six Dynasties period (六朝; 220–589 CE). Produced during this era, the jar (HKU.C.1969.0334) is distinguished by its finely incised exterior decoration. In particular, the lotus petals on the upper body suggest a Buddhist connection. Lotus petals symbolise creation, renewal and purity in Buddhist ideology. As Li (1996) points out, the inclusion of lotus elements in stylised patterns associated with Buddhism first occurred on ceramics during the Six Dynasties. During the later Tang dynasty (唐朝, 618–907 CE), Buddhism established itself as China’s predominant faith, and its influence is evident throughout Chinese art, poetry and other cultural artefacts.

佛教的傳播是六朝時期(公元220-589年)最重要的社會文化變化之一。 在這個時代生產的青釉罐(HKU.C.1969.0334),以精細的裝飾著稱。此青釉罐罐身的蓮瓣紋,顯示出器皿與佛教的關聯。在佛教思想中,蓮花花瓣象徵創造,更新與純潔。 正如Li(1996)所指出,與佛教信仰相關的蓮花圖案,在六朝時期的陶瓷上首先出現。在唐朝(公元618-907年),佛教成為中原的主要信仰,其影響力在整個地區的藝術,詩歌和其他文化手工藝品中都顯而易見。
Jar: two lugs, Tang dynasty (618–907 CE), Stoneware with celadon glaze, HKU.C.1953.0032
雙繫罐,唐代 (618–907 CE),綠釉炻器.HKU.C.1953.0032
Following the end of the Sui dynasty (隋朝; 581–618 CE), a rapid decline in the production of older forms of Yue ware led to key stylistic changes during the Tang dynasty. The clay used for ceramics became more finely grained, while the vessels became more elegantly shaped and elaborately designed (Sato, 1981). This jar (HKU.C.1953.0032) was created in the Tang dynasty. The celadon vessel has a globular shape and a pair of handles. The two loop handles are symmetrically located on either side of the jar’s shoulders pointing upwards. The vessel is completely covered inside and out with a fine, greyish-green glaze, except for the base.
During the Tang dynasty, potters at the Yue kilns developed a new technique in which they would fire ceramics in air-tight firing chambers, which prevented the glaze from becoming re-oxidated (Chen, 2004). When oxygen enters into the chamber during firing, the glazes mature into an olive-green instead of a bluish-green—the glaze colour of the mysterious mise (or bise, 秘色 secret colour) ware. In addition to its wondrously beautiful glaze colour, mise used smoother clay bodies and glaze materials. 14 examples of Yue ceramics that can be firmly identified as mise wares were excavated in 1987 in a crypt beneath the stupa of the Famen Temple (法門寺) in Shaanxi. These objects are undecorated and characterised by a thin layer of light blueish-green glaze; their shapes also differ from other contemporary forms of Yue ware. The fine quality of mise wares has mesmerised literati, collectors, poets and emperors since the Tang dynasty. Their earliest known mention appears in a poem by the poet Lu Guimeng (陸龜蒙; ?–881) called ‘Mise Yueqi’ (秘色越器; Secret Celadon from the Yue Kilns): ‘Amidst the wind and dew of deepest autumn, the Yue kilns opened once again, as the celadon captures the lively green shade of 1,000 hills,’ (「九秋風露越窯開,奪得千峰翠色來。」). Many questions remain unanswered regarding the mise pieces from the Famen Temple, such as why this enormously successful style was not further developed by the Yue potters. Largely due to increased competition, the Yue kilns fell into decline in the Northern Song dynasty following its peak in the Tang, and then ceased production altogether in the Southern Song.
.
在隋朝(581-618年)衰亡後,舊式越窯器的生產迅速下滑,致使越窯器的風格在唐代發生了重大變化。在唐朝時期,用於越窯器陶體的粘土顆粒變得更為幼細,而器物的形狀變得更為優雅,設計也更為別緻(Sato,1981)。 這一件於唐朝製成的雙繫罐(HKU.C.1953.0032), 其罐身呈球狀,並附有一對位於罐肩兩側的環形小柄。除罐身底部外,該容器的內部和外部都覆有光滑細膩、青翠奪目的青釉。
在唐代,越窯工匠開發出一種嶄新的燒製技術,他們通過在不透氣的燒成室中燒製陶器,從而防止釉料被再度氧化(Chen,2004年)。在燒成的過程中,當氧氣進入窯室時,釉料會演變成橄欖綠色,而非秘色瓷器具有的藍綠釉色。秘色越器除了具有令人驚艷的釉色,更有著較細膩的粘土土體。 1987年,在陝西法門寺佛塔下的一個地下室中,挖掘出14件被確定為秘色瓷器的越窯器。這些秘色瓷未經特殊裝飾,其主要特徵是具有一層淺薄的淡藍綠色釉料,而瓷器的形狀也與其他越窯器物不同。自唐朝以來,文人、收藏家、詩人和帝皇對品質絕佳的秘色瓷器,都有著深深的著迷。秘色瓷器最早於詩人陸龜蒙(?–881)的一首名為《秘色越器》的詩中提到:「九秋風露越窯開,奪得千峰翠色來。」。目前尚有許多關於法門寺的秘色瓷器的不解之謎,例如為何越窯工匠沒有更進一步發展這種備受追棒的瓷器風格。主要由於競爭加劇,越窯器在唐朝達到高峰之後,在北宋開始衰落,繼而在南宋完全停產。

III. Changsha and Yaozhou Celadons from
the Five Dynasties to the Northern Song
III. 五朝至北宋期間的長沙與耀州窯青釉器
Jar, Five Dynasties period (907–960 CE), Stoneware with celadon glaze, Gift of Brian McElney, HKU.C.1978.0633
罐,五代 (907–960 CE),綠釉炻器.Brian McElney惠贈,HKU.C.1978.0633
Made in the Five Dynasties period (五代; 907–960 CE), this large jar (HKU.C.1978.0633) is covered in a thin, brownish-green glaze that features a pair of handles depicting the head of a mysterious creature. This vessel was produced by artisans in the Changsha (長沙) district, one of the major kiln sites in Southern China. Changsha ware (長沙窯器) was first produced in the eighth century, reaching its peak in the mid- to late Tang. Based on the distinct similarities between Changsha and early Yue ceramics, it is generally believed that Changsha wares were modelled on the earlier Yue forms.
In its prime, Changsha wares were produced in large quantities and exported to countries around the globe via the overland Silk Road and maritime trading routes. Thousands of Changsha objects were excavated from a shipwreck near Belitung in Indonesia, attesting to the sheer scale of the early trade of Chinese ceramics and the history of globalism. Due in part to the military chaos and political instability of the Five Dynasties period, quality declined gradually following the end of the Tang dynasty, while export production ceased altogether in the mid-tenth century.
這個大罐(HKU.C.1978.0633)製於五代時期(公元907–960年),表面施上一層薄薄的棕綠色釉料,兩側附有一對描繪神秘生物頭部的提手。這件器物是由長沙地區的陶匠所製。長沙是中國南方主要的窯址之一。長沙窯器創於公元八世紀,並在唐代中後期達到頂峰。由於長沙窯器與最初的越窯器相似,因此長沙窯器被認為是在早期越窯器的基礎上發展而成。
於全盛時期,長沙窯器大量生產,並透過陸上絲綢之路和海上貿易路線出口至世界各地。過去曾在印尼勿里洞附近的一艘沉船中,挖掘了過千件的長沙器物,足以證明早期中國陶瓷的貿易規模龐大,及其全球化的歷史。由於五代時期的軍事混亂和政治動盪,導致長沙窯器的質量於唐朝末期逐漸下降,而出口生產更於十世紀中葉完全停頓下來。

The Belitung cargo in situ. Source: Michael Flecker.
印尼勿里洞沉船遺址. Source: Michael Flecker.

Dish: floral design, Northern Song dynasty (960–1127 CE), Stoneware with celadon glaze, HKU.C.1954.0107
碟: 花卉紋,北宋 (960–1127 CE),綠釉炻器.HKU.C.1954.0107
Around the tenth century, kilns in the Yaozhou (耀州) district began producing a variety of celadon objects known as Yaozhou ware (耀州窯器). Also referred to as ‘northern celadon’, these objects were produced in kilns in Shaanxi province, as well as in Linru and Baofeng in Henan province. From the late 10th century onwards, Yaozhou potters used visibly greener glazes (Wood, 1999). Yaozhou ceramics were primarily fired in brick-built, horseshoe-shaped and coal-fired mantou kilns (饅頭窯). A typical reduction firing temperature at Huangbao (黃寶鎮), one of the main Yaozhou kiln sites, was approximately 1300°C (Wood, 1999).
This Yaozhou celadon dish (HKU.C.1954.0107) produced in the Northern Song period (960–1127 CE) is finely potted with wide flared sides raised on a narrow foot. The dark olive-toned glaze covers the bowl both inside and out, exhibiting a wondrous lustre. The bowl’s interior is carved and incised with floral decorations, while the contrasting dark and light areas are the result of the glaze sinking into deeply carved depressions. According to Wood (1999), ‘lime-alkali’ glazes were used. These glazes remain stable when fired at high temperatures, which allows the glaze to obtain its signature olive-green transparency. This method is ideal for displaying delicate carving and other decorative elements. Scientific analysis shows that Yaozhou celadon glazes contain about twice as much iron and titanium oxide as later Longquan celadons, and the fine olive-green tones owe much to the higher concentration of oxides (Wood, 1999) .
大約於公元十世紀,耀州地區的窯爐開始燒製各種青瓷器。這類青瓷被稱頌為「耀州窯器」或「北方青瓷」,在陝西省以及河南省的臨汝和寶豐縣的眾多窯爐中都有生產。從十世紀後期開始,耀州的陶工使用了色澤明顯較綠的釉料(Wood,1999)。耀州窯器多以由磚塊砌成,呈馬蹄形,並使用煤為燃料的饅頭窯燒造而成。耀州窯的主要窯場之一的「黃寶鎮」窯區,普遍把窯溫提升至攝氏1,300度來達到還原燒成的效果(Wood,1999)。
此耀州青瓷碟製於北宋時期(公元960年至1127年),造型精細,矮圈足,且侈口外溢,近口沿處寬闊開敞。瓷碟從裡到外施上深橄欖色的釉料,展現出奇妙的光澤。碗的內部雕有花卉圖紋,而瓷器上深色和淺色區域的對比是釉沉入雕刻凹陷處中的結果。Wood(1999)的研究指出,這類青瓷器沿用了石灰鹼釉。這種釉料在高溫下燒製時,仍能保持穩定,呈現出其具標誌性的剔透感,蒼翠欲滴。石灰鹼釉的運用,有助把精美的雕刻和其他紋飾元素清晰地映現出來。有科學分析顯示,耀州青瓷中的釉料所含的鐵和二氧化鈦是後來的龍泉青瓷的兩倍,而意境清新的橄欖色則是由其含量較高的氧化物促使而成(Wood,1999)。
Bowl: flowers, Northern Song dynasty (960–1127 CE), Stoneware with celadon glaze, HKU.C.1959.0223
碗: 花卉紋,北宋 (960–1127 CE),綠釉炻器.HKU.C.1959.0223

This Yaozhou celadon bowl (HKU.C.1959.0223) was also produced during the Northern Song. The exterior surface is plain, while the interior is carved with scrolling peonies. The interlacing stems and leaves spread out and cover the surface in an elegantly fluid motion. The refined and rhythmic lines that form the blossom gracefully unfurl along the bowl’s interior surface. For centuries, people of all classes were enthralled by the beauty and fragrance of the peony. ‘Only the peony is worthy of being called “Beauty of the Empire”’—the Tang poet Liu Yuxi (劉禹錫) proudly proclaimed in one of his poems. The peony also has been known as the ‘flower of riches and honour’ and remains one of the most popular decorative motifs.
此耀州青瓷碗同樣製於北宋時期(HKU.C.1959.0223)。碗外平滑樸實,而碗內則雕有牡丹圖紋。當中的莖和葉互相交織,周密無際,以優雅的流線覆蓋着碗的內面。精緻而具節奏感的線條繪織成花卉,沿著碗的內面優美地張開起來。數個世紀以來,各個階層的人們都深受牡丹的雍容和芬芳著迷。 唐代詩人劉禹錫在詩作《賞牡丹》中更宣稱:「唯有牡丹真國色,花開時節動京城。」牡丹也享有「財富和榮譽之花」的盛名,至今仍然是最受歡迎的裝飾圖紋之一。
Bowl: flowers, Northern Song dynasty (960–1127 CE), Stoneware with celadon glaze, Gift of Mr. Dunt King, HKU.C.1976.0618
碗: 花卉紋,北宋 (960–1127 CE),綠釉炻器.金重德先生惠贈,HKU.C.1976.0618
Produced during the Northern Song, this bowl (HKU.C.1976.0618) is another fine example of Yaozhou celadon wares. The vessel is completely covered with a light olive-green glaze, and its interior is carved with chrysanthemum blossoms along a leafy scroll. Based on the length of their bloom, chrysanthemums have been traditionally associated with longevity in Chinese culture. The diverse and rich techniques applied to create the decorative representations of peonies, chrysanthemums and other motifs show the high level of craftsmanship of Yaozhou potters.
此碗(HKU.C.1976.0618)製於北宋時期,是另一件耀州青瓷的好例子。瓷器被淺淡的橄欖綠色釉完全覆蓋,內部則雕有正在綻放的菊花,與茂盛的綠葉相映成趣。由盛開的花卉長度可見,菊花在傳統中國文化中擁有寓意長壽的象徵意義。耀州陶工的工藝水平高超非凡,能以多樣而豐富的技巧,描繪牡丹、菊花和其他裝飾圖紋。

IV. Guan and Longquan Celadons from the
Song and Yuan Dynasties
IV. 宋元兩代的官窯和龍泉窯青釉器
Bowl, Song dynasty (960–1279 CE) or Yuan dynasty (1271–1368 CE), Stoneware with crackled celadon glaze, HKU.C.1966.0303
碗: ,宋代 (960–1279 CE) 或 元代(1271–1368 CE),青釉紋片炻器.HKU.C.1966.0303
With its diverse techniques, elegant forms and mesmerising range of glaze colours, Chinese ceramics reached their peak during the Song dynasty (960–1279 CE). Buoyed by economic prosperity, national peace and the rise of the scholar-official (士大夫) class, ceramic industries in China thrived at unprecedented levels. To commemorate these ceramic wares, and to ensure their heritage, connoisseurs and literati in the Ming and Qing dynasties canonised the so-called ‘Five Great Kilns’ (五大名窯) of the Song dynasty: the Ru (汝), Jun (鈞), Guan (官), Ding (定) and Ge (哥). Only the Ding kiln did not use celadon glazes. The development of Guan ware (官窯器) was the result of a royal initiative—Guan means ‘official’ in Chinese. Following the invasion of the north and the flight of Emperor Gaozong of the Song (宋高宗) to establish the Southern Song at a new capital, the imperial court lost access to the northern kilns, including Ru and Jun. The Guan kiln was therefore developed as a southern version of the famous Ru kiln.
Produced by potters working at the Guan kiln site, this elegantly shaped bowl (HKU.C.1966.0303) is coated with a fine layer of icy green glaze with blue undertones. Further underscoring its artisanal marvel, the surface glaze presents a random network of crackles. This widely admired glaze effect occurs during firing and is achieved when the glaze and body shrink at different rates. According to Medley (1989), this effect arises during the cooling process, when the thermal expansion differs between the body and glaze. As expansion during heating is matched by the contraction that occurs during cooling, a ‘high expansion’ glaze will contract significantly as it cools. If this shrinkage is greater than the underlying clay body, the glaze will crackle during the cooling stage (Wood, 1999). Variances in kiln temperatures and environments account for the variations in glaze colour and lines, with the glazes becoming ‘icier’ and more heavily crazed as the firing temperature increases (Wood, 1999). Despite its diminutive size, this bowl is notable for its translucency, thickness and captivating blueish-green tones.
中國陶瓷在宋代達到了巔峰,展現出多樣的工藝技巧、優雅的形態和令人著迷的釉料色域。在經濟繁榮、國家和平穩定和士大夫階級興起的推動下,中國的陶瓷工業蓬勃發展,達到空前水平。為了紀念宋代陶瓷並確保其文化傳承,明清兩代的鑑賞家和文人將宋代的最出色的五個窯口統稱為「五大名窯」,包括 「汝」、「鈞」、「官」、「定」和「哥」窯,而當中只有定窯一口並不使用青釉。官窯器的發展是由皇室所倡導 —「官」在中文意為「官方」。隨著北部被金人攻入及佔領,宋高宗向下逃亡至新都建立南宋。皇室因此失去了包括汝窯和鈞窯在內的北方窯口,而官窯正正是以模仿著名的汝窯而在南方發展而成的窯口。
這隻形狀優美的碗(HKU.C.1966.0303)由官窯的陶工所製,表面施有一層具藍色基調,晶瑩剔透的青釉。釉面上的冰裂紋碧翠怡人,器形巧緻雅絕。這種廣受青睞的釉層冰裂在燒製過程中發生,是只有當釉料和坯體以不同的速率收縮拉扯時才可以達到的效果。Medley(1989)的研究指出,這種冰裂效果是在冷卻過程中,當坯體和釉料因為彼此的冷縮熱脹存在差異時而產生的。燒製過程中的膨脹與冷卻過程中的收縮雙管齊下,令膨脹係數高企的釉層於冷卻時顯著收縮。一旦釉層的收縮大於坯體的收縮,釉層便會如冰破裂,裂片層疊(Wood,1999)。窯爐於溫度和環境上的差異使釉層的顏色和線條出現變化,釉層漸趨「冰瑩」,並隨著焙燒溫度升高,越發帶勁的產生裂紋(Wood,1999)。儘管此碗玲瓏小巧,卻以其清澈的表面、厚實的質感和迷人的藍綠色調而格外引人注目。
Bowl, Southern Song dynasty (1127–1279 CE), Stoneware with crackled celadon glaze, HKU.C.1990.0931
碗: ,南宋 (1127–1279 CE),青釉紋片炻器.HKU.C.1990.0931
Encapsulating the Song’s refined aesthetics, this celadon bowl (HKU.C.1990.0931) is another remarkable example of Guan celadon objects manufactured in the Southern Song dynasty. The bowl’s smoothly rounded sides are suffused with randomly crackled, golden glaze lines, and the reddish-brown ceramic body shows through the unglazed foot ring. Analyses of Guan ware glazes suggest that their recipes were likely mixtures of aluminous porcelain stone with wood ash and/or limestone (Wood, 1999). While the end date of the Guan kiln is unknown, the site likely continued to produce ceramics at least until the Ming dynasty (明朝; 1368–1644).
此碗(HKU.C.1990.0931)完美演繹了宋代的精緻美學,是南宋時期於官窯製造的另一件傑出青瓷器。碗上圓滑的表面佈滿了不規則的冰裂和金絲鐵線紋。觀者更可以從其未上釉的圈足略窺紅棕色的粘土土體。有官窯釉料的分析顯示,它們是由鋁質瓷石與木灰和/或石灰石混合而成(Wood,1999)。雖然官窯確實的沒落仍舊是一個謎,但該窯口應該至少在明朝(公元1368–1644年)之前仍在燒製陶瓷。
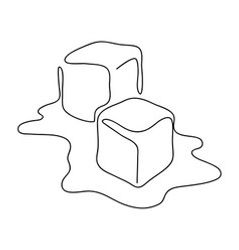
Bowl, Southern Song dynasty (1127–1279 CE), Stoneware with crackled celadon glaze, HKU.C.1959.0224
碗: ,南宋 (1127–1279 CE),青釉紋片炻器.HKU.C.1959.0224
Crackle glazing produced in the Guan kilns are some of the most widely admired and imitated styles in China, and the imitations began quite early, most notably at the southern kiln sites that produced Longquan ware (龍泉窯器; HKU.C.1959.0224). The crackle lines on this Longquan bowl were deliberately made to resemble the celebrated glazes of Guan celadons. Ming scholar Cao Zhao’s (曹昭) celebrated antiquarian guide for China’s material culture Gegu Yaolun (格古要論) states that during the Song dynasty, ‘the facsimiles of official kiln wares were all made at the Longquan kiln’. This example epitomises the ceramics produced near the Southern Song capital that re-created imperial wares for the court, while illustrating the technical prowess of Longquan potters for imitating ceramics that conformed to courtly taste.
官窯生產的冰裂瓷器在中國廣受追棒,並被爭相仿效。官窯冰裂瓷器的仿製品很早便出現,尤其是在生產龍泉窯器的南部窯口。這隻龍泉碗(HKU.C.1959.0224)上的冰裂紋刻意仿照享負盛名的官窯冰裂。明代學者曹昭曾撰寫《格古要論》,為當時明代一部著名的收藏指南。曹昭指出,於宋朝時期,「官窯⋯ ⋯偽者皆龍泉燒。」若要一窺南宋首都附近生產的龍泉窯器,這隻碗便是最佳的例子。這隻龍泉碗模仿了為宮廷而製的官窯器具,同時還展示了龍泉窯的陶工如何輕而易舉地仿製出迎合宮廷品味的陶瓷,具有非凡的實力與技術。
Lobed bowl, Late Southern Song (1127–1279 CE) or early Yuan dynasty (1271–1368 CE), 13th or 14th century,
Stoneware with celadon glaze, HKU.C.1955.0158
花瓣形碗: ,南宋 (1127–1279 CE)末 或 元 (1271–1368 CE) 初,青釉炻器.HKU.C.1955.0158
Made in Zhejiang, early Longquan ceramics bear a remarkable resemblance to the famous Yue wares in terms of their glaze, potting and decoration (Tregar, 1982). During the Song dynasty, Longquan wares were not used by the imperial court, in contrast to the celadon items manufactured in the northern kilns (Vainker, 1998). The literati were presumably the primary connoisseurs of Longquan ceramics. In addition to objects made for daily use, Longquan ceramics were sometimes used on altars and as part of burials. This Longquan celadon bowl (HKU.C.1955.0158) is characterised by its six-lobed mouth rim. The rounded sides rise from a straight foot covered evenly with a jade-toned glaze; the unglazed foot ring reveals its brown clay body.
早期的龍泉瓷器是在浙江製造的。不論在釉料、陶器或圖紋裝飾方面,都與著名的越窯器十分相似(Tregar,1982)。有別於在北方窯口所生產的青瓷製品,龍泉瓷器未有被宋朝皇室使用(Vainker,1998)。龍泉瓷器的主要鑑賞家大概是文人雅仕。除了日常使用的物品外,龍泉瓷器有時還用於祭壇和墓葬之中。這隻龍泉青瓷碗(HKU.C.1955.0158)的特徵是其口沿呈六瓣葵花式,斜深壁,施上均勻的翡翠色釉料,觀者更可以從其未上釉的圈足略窺棕色的粘土土體。

Additional Resources
Address: 90 Bonham Road, Pokfulam, Hong Kong View the location on Google Maps
Tel: (852) 2241 5500 Fax: (852) 2546 9659 Email: museum@hku.hk
© 2022 by University Museum and Art Gallery, HKU. All Rights Reserved